Quality Control
NPC Eelctric is committed to the principle of "quality first and continuous improvement," striving to provide our customers with stable and reliable wire & cable products as well as various types of transformers. Our company has established a comprehensive quality management system, strictly implemented in accordance with ISO 9001 standards. From raw material procurement and production process control to final product inspection, every step is carefully monitored to ensure quality.
Boths of our production will be follow the ISO quality control strand, follow the Routine test,Progress test under manufacturer and Finally Factory test before shippment.
In addition, we cooperate with third-party laboratories that are UL certified and accredited to ISO/IEC 17025 standards, such as the Suzhou Testing Institute, to ensure our product performance meets international requirements. Our in-house quality control team is also equipped to conduct full-process traceability and quality evaluations, ensuring that every batch of products meets customer expectations before delivery.
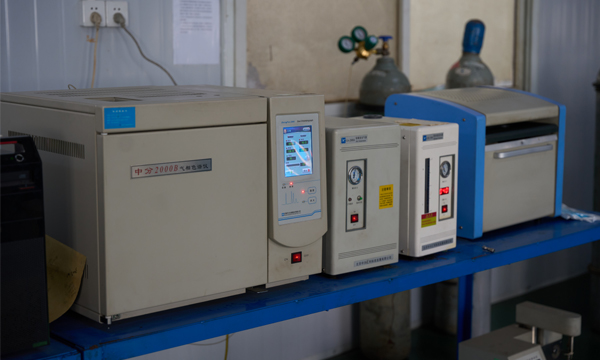
01
Raw Material Test
At NPC Electric, we place great emphasis on the quality of raw materials, as they are the foundation of reliable and high-performance products. We have strict requirements for all incoming materials, including aluminum, copper, insulation materials, and outer sheath compounds.
Before any material enters the production line, it must pass a full range of quality tests conducted by our in-house technical team. These tests include:
01:The conductor raw material Copper or Aluminum will be test as below items:
Visual Inspection: Check for surface defects such as oxidation, scratches, or fractures.
Resistivity Test: Measure the electrical performance of the conductor IEC or ASTM standards).
Chemical Composition Analysis: Verify the purity of copper or aluminum (typically required to be above 99.9%).
Dimensional Inspection: Ensure the diameter, ovality, and other dimensions meet the specified standards.
Mechanical Performance Test: Evaluate tensile strength, elongation, and other mechanical properties.
02:Silicon Steel Sheets (for Transformer Cores)
Coating Inspection: Check the integrity of the anti-rust coating.
Magnetic Property Testing: Evaluate core loss and magnetic flux density (B-H curve).
Thickness and Width Measurement: Ensure dimensional accuracy for proper lamination.
Grain Orientation Test: Confirm whether the sheets are grain-oriented silicon steel.
03:The oil will be test as below items:
Breakdown Voltage Test: Tests the ability of oil to break down under high voltage, reflecting whether its insulation performance is good.The test result should be ≥ 45 kV(as ASTM D6871/IEEE C57.147 )
Moisture Content: Moisture will greatly reduce the insulation performance of the oil and increase the risk of breakdown.
Dielectric Dissipation Factor: Reflects the insulation aging and impurity level of the oil, the lower the value, the better.
Acidity Test: Detects acidic substances after oil oxidation. A high acid value indicates that the oil has deteriorated.
Color and Visual Inspection: Check whether the oil has discoloration, precipitation or suspended impurities. Generally, it is required to be a light yellow transparent liquid.
Dissolved Gas Analysis: Analyze the gas components dissolved in the oil to determine whether the transformer has internal faults (such as overheating, discharge, breakdown).
Interfacial Tension: Reflects the cleanliness and aging of the oil. The higher the value, the better.
Flash Point: Ensure the safety of the oil at high temperatures, usually > 135°C.
Before any material enters the production line, it must pass a full range of quality tests conducted by our in-house technical team. These tests include:
01:The conductor raw material Copper or Aluminum will be test as below items:
Visual Inspection: Check for surface defects such as oxidation, scratches, or fractures.
Resistivity Test: Measure the electrical performance of the conductor IEC or ASTM standards).
Chemical Composition Analysis: Verify the purity of copper or aluminum (typically required to be above 99.9%).
Dimensional Inspection: Ensure the diameter, ovality, and other dimensions meet the specified standards.
Mechanical Performance Test: Evaluate tensile strength, elongation, and other mechanical properties.
02:Silicon Steel Sheets (for Transformer Cores)
Coating Inspection: Check the integrity of the anti-rust coating.
Magnetic Property Testing: Evaluate core loss and magnetic flux density (B-H curve).
Thickness and Width Measurement: Ensure dimensional accuracy for proper lamination.
Grain Orientation Test: Confirm whether the sheets are grain-oriented silicon steel.
03:The oil will be test as below items:
Breakdown Voltage Test: Tests the ability of oil to break down under high voltage, reflecting whether its insulation performance is good.The test result should be ≥ 45 kV(as ASTM D6871/IEEE C57.147 )
Moisture Content: Moisture will greatly reduce the insulation performance of the oil and increase the risk of breakdown.
Dielectric Dissipation Factor: Reflects the insulation aging and impurity level of the oil, the lower the value, the better.
Acidity Test: Detects acidic substances after oil oxidation. A high acid value indicates that the oil has deteriorated.
Color and Visual Inspection: Check whether the oil has discoloration, precipitation or suspended impurities. Generally, it is required to be a light yellow transparent liquid.
Dissolved Gas Analysis: Analyze the gas components dissolved in the oil to determine whether the transformer has internal faults (such as overheating, discharge, breakdown).
Interfacial Tension: Reflects the cleanliness and aging of the oil. The higher the value, the better.
Flash Point: Ensure the safety of the oil at high temperatures, usually > 135°C.
View More
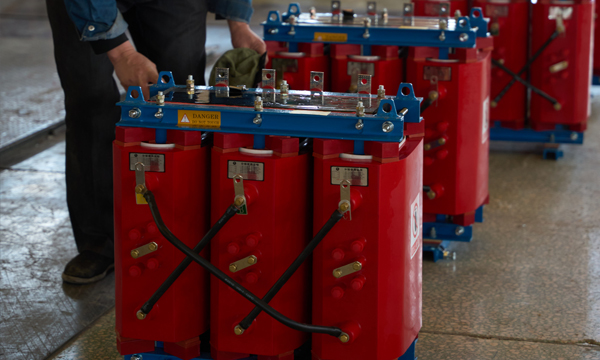
02
Manufacturer Progress Test
NPC Electric has a dedicated team to follow up on in-process testing during manufacturing. All tests will be conducted as follows:
1. Coil winding process inspection
Check whether the type and specification of the wire meet the requirements of the drawing
The number of turns, layers and dimensions of the winding are accurate
The winding tension is consistent, whether there is looseness, random winding or short circuit
The marking and treatment of the intermediate point, tap and end are correct
2. Coil insulation inspection
The interlayer insulation is complete and the thickness is sufficient
The inter-turn paper package/wrap is misaligned or wrinkled
The wire welding and connection points are smooth and burr-free
3. Core assembly inspection
Neatness of silicon steel sheet stacking
The core gap and fasteners are firmly installed
The core grounding treatment is standardized (single-point grounding)
The insulation installation position is correct
4. Coil and core set inspection
The set gap is reasonable, whether there is crushing and friction
The relative position of the coil and the core is centered
The coil is firmly fixed and whether there is a risk of loosening
5. Drying process detection (vacuum drying or hot air drying)
Record drying temperature, time, vacuum degree and other process parameters
6. Oil filling process inspection (applicable to oil-immersed transformers)
Oil cleanliness, temperature, oil filling speed control
Vacuum oil filling, whether oil filling is full
The standing time after oil filling meets the requirements
7. Intermediate electrical performance test (as needed)
Turn-to-turn withstand voltage test
Loop resistance test
No-load and On--load loss
8. Assembly process inspection
Correctness and clarity of lead wiring
Enclosure sealing, mounting hole position and fixture integrity
Correctness of installation of bushings, oil level gauges, thermostats and other components
1. Coil winding process inspection
Check whether the type and specification of the wire meet the requirements of the drawing
The number of turns, layers and dimensions of the winding are accurate
The winding tension is consistent, whether there is looseness, random winding or short circuit
The marking and treatment of the intermediate point, tap and end are correct
2. Coil insulation inspection
The interlayer insulation is complete and the thickness is sufficient
The inter-turn paper package/wrap is misaligned or wrinkled
The wire welding and connection points are smooth and burr-free
3. Core assembly inspection
Neatness of silicon steel sheet stacking
The core gap and fasteners are firmly installed
The core grounding treatment is standardized (single-point grounding)
The insulation installation position is correct
4. Coil and core set inspection
The set gap is reasonable, whether there is crushing and friction
The relative position of the coil and the core is centered
The coil is firmly fixed and whether there is a risk of loosening
5. Drying process detection (vacuum drying or hot air drying)
Record drying temperature, time, vacuum degree and other process parameters
6. Oil filling process inspection (applicable to oil-immersed transformers)
Oil cleanliness, temperature, oil filling speed control
Vacuum oil filling, whether oil filling is full
The standing time after oil filling meets the requirements
7. Intermediate electrical performance test (as needed)
Turn-to-turn withstand voltage test
Loop resistance test
No-load and On--load loss
8. Assembly process inspection
Correctness and clarity of lead wiring
Enclosure sealing, mounting hole position and fixture integrity
Correctness of installation of bushings, oil level gauges, thermostats and other components
View More
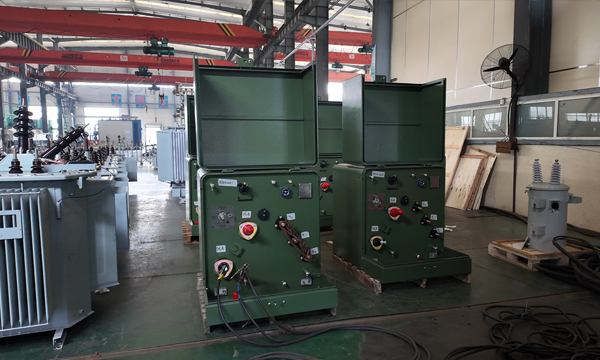
03
Routine Test Before Shippment
1. Visual Inspection: Ensure that the transformer has no physical defects, such as damage, scratches, or leaks.
Items Checked: Nameplate data, external parts, and physical condition of the transformer.
2. Turn Ratio Test: Verify that the voltage ratio between the primary and secondary windings is correct, ensuring the transformer’s voltage conversion is accurate.
3. Winding Resistance: Verify that the resistance of the windings is within the expected range, ensuring that there are no short circuits or broken windings.
Test Method: Use a micro-ohmmeter or other resistance measurement tools to measure the resistance of windings.
4. Insulation Resistance Test: Ensure that the insulation between the windings and ground is sufficient and there is no leakage.
Test Method: Apply a high voltage (typically DC 5kV) to measure the resistance between the windings and ground.
5. No-load Loss and Current Test: Measure the no-load loss and current to ensure the transformer performs efficiently under no-load conditions.
Test Method: Apply rated voltage to the transformer and measure the current and power loss.
6. Short-circuit Impedance Test: Measure the impedance of the transformer under short-circuit conditions to check for correct impedance and load characteristics.
Test Method: Apply a reduced voltage to the transformer to simulate short-circuit conditions and measure the resulting current and voltage drop.
7. Dielectric Strength Test (High Voltage Test)
Purpose: Ensure the transformer’s insulation can withstand high voltages without breakdown.
Test Method: Apply high-voltage tests between the windings, and between windings and ground, to check the dielectric strength.
8. Oil Test (for Oil Transformers): Check the quality of the transformer oil for insulation and dielectric properties.
Test Method: Perform tests like the dielectric strength, water content, and acidity of the oil.
9. Temperature Rise Test: Check the transformer’s temperature rise under full load conditions to ensure that it operates within safe temperature limits.
Test Method: Run the transformer under full-load conditions and measure temperature rises at key points.
10. No-load Loss and Current Test: Test the no-load loss and current to ensure that the transformer’s efficiency is within specifications when no load is applied.
Test Method: Apply rated voltage to the transformer and measure the no-load current and losses.
11. Sound Level Test: Ensure that the transformer’s noise level is within acceptable limits.
Test Method: Measure the noise level produced by the transformer during operation.
12. Vibration Test: Ensure that the transformer does not produce excessive vibrations during operation that could cause damage or affect performance.
Test Method: Use vibration sensors to monitor and measure vibrations during operation.
13. Protection Device Testing: Verify that the transformer’s protection devices, such as overcurrent protection and temperature sensors, are functioning correctly.
Test Method: Simulate fault conditions and test the response of protection mechanisms.
Items Checked: Nameplate data, external parts, and physical condition of the transformer.
2. Turn Ratio Test: Verify that the voltage ratio between the primary and secondary windings is correct, ensuring the transformer’s voltage conversion is accurate.
3. Winding Resistance: Verify that the resistance of the windings is within the expected range, ensuring that there are no short circuits or broken windings.
Test Method: Use a micro-ohmmeter or other resistance measurement tools to measure the resistance of windings.
4. Insulation Resistance Test: Ensure that the insulation between the windings and ground is sufficient and there is no leakage.
Test Method: Apply a high voltage (typically DC 5kV) to measure the resistance between the windings and ground.
5. No-load Loss and Current Test: Measure the no-load loss and current to ensure the transformer performs efficiently under no-load conditions.
Test Method: Apply rated voltage to the transformer and measure the current and power loss.
6. Short-circuit Impedance Test: Measure the impedance of the transformer under short-circuit conditions to check for correct impedance and load characteristics.
Test Method: Apply a reduced voltage to the transformer to simulate short-circuit conditions and measure the resulting current and voltage drop.
7. Dielectric Strength Test (High Voltage Test)
Purpose: Ensure the transformer’s insulation can withstand high voltages without breakdown.
Test Method: Apply high-voltage tests between the windings, and between windings and ground, to check the dielectric strength.
8. Oil Test (for Oil Transformers): Check the quality of the transformer oil for insulation and dielectric properties.
Test Method: Perform tests like the dielectric strength, water content, and acidity of the oil.
9. Temperature Rise Test: Check the transformer’s temperature rise under full load conditions to ensure that it operates within safe temperature limits.
Test Method: Run the transformer under full-load conditions and measure temperature rises at key points.
10. No-load Loss and Current Test: Test the no-load loss and current to ensure that the transformer’s efficiency is within specifications when no load is applied.
Test Method: Apply rated voltage to the transformer and measure the no-load current and losses.
11. Sound Level Test: Ensure that the transformer’s noise level is within acceptable limits.
Test Method: Measure the noise level produced by the transformer during operation.
12. Vibration Test: Ensure that the transformer does not produce excessive vibrations during operation that could cause damage or affect performance.
Test Method: Use vibration sensors to monitor and measure vibrations during operation.
13. Protection Device Testing: Verify that the transformer’s protection devices, such as overcurrent protection and temperature sensors, are functioning correctly.
Test Method: Simulate fault conditions and test the response of protection mechanisms.
View More
Technical Advantages
● 30+ years of manufacturing experience
● ISO and UL certified production
● Customized cable and transformer solutions
Our Factory
Our Partners
Welcome your inquiry
Honesty, Integrity, Frugality, Activeness and Passion